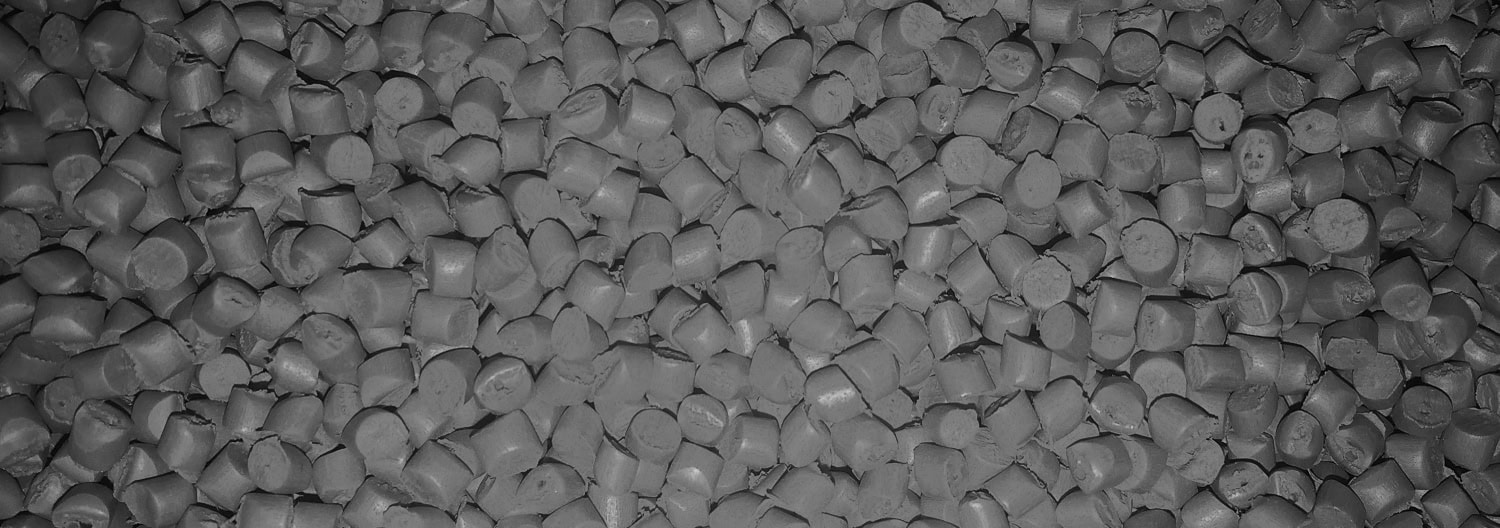
There are many polymers that can be used to mould your products, with each one having its own benefits depending on the final use of the part. Firstly it’s best to understand the terms used, what they mean and the differences between them before we talk about specific polymers for your project.
A plastic is any natural, synthetic or semi-synthetic material that can be shaped when soft. Amber and wood are naturally occurring materials that display plasticity. In the case of injection moulding, we are referring to thermoplastic materials that are heated, injected into a mould and then allowed to cool to form stable products.
A material that becomes soft and pliable when heated and solidifies when cooled. The heating/cooling process can be repeated many times, with no permanent change in the structure after the application of heat. This means they can, theoretically, be recycled an infinite number of times.
Thermoplastics are typically used to produce parts by various moulding processes, such as injection moulding, blow moulding and extrusion.
A thermoplastic elastomer (TPE) is a copolymer or a polymer blend (usually a plastic and a rubber) that consists of materials with both thermoplastic and elastomeric properties.
TPEs are commonly used in products that would have previously been made from thermoset elastomers (rubber). In contrast to thermoset elastomers, TPEs are easier to injection mould and take less time and energy to process. Just like other thermoplastics, this process is reversible and the products are recyclable.
A polymer is a substance consisting of very large molecules (macromolecules). They are created through the polymerisation of many small molecules (monomers). There are naturally occurring polymers (such as DNA) and synthetic polymers (such as nylon).
A molecule of low molecular weight that can react with identical or different molecules of low molecular weight to form a larger polymer in a polymerisation process, e.g. methane.
A material that becomes permanently formed when heated, so the injection process is irreversible for these materials. As thermosets are irreversibly altered by the hardening process, thermosets aren’t recyclable. Bakelit is probably the most well-known thermoset. MGS does not work with thermosets.
A polymer produced by polymerising a single monomer. Common examples include polystyrene, polycarbonate, and low-density & high-density polyethylene.
A polymer produced by polymerising two or more monomer types. Copolymers can be classified based on how these polymers are arranged along the chain - there are two main types, branched and linear.
Common examples of co-polymers include polyvinyl chloride (PVC), styrene-acrylonitrile (SAN), PTFE and ABS.
A mixture of two or more polymers to create a new material with different physical properties.
Depending on the compatibility of the polymers, the properties of the blend can surpass that of its component parts. Incompatible polymers can be mixed if a coupling agent is used. Common examples of Polymer Blends are PC/ABS, PA/ABS and PC/PET.
A thermoplastic’s properties can also be modified by adding a filler.
Fillers include (but are not limited to): glass fibre or bead, to improve the dimensional stability when cooling and also add strength to the product; EPDM, which can increase the toughness of a component; anti-static additives, which reduce the chance of electrostatic build-up and thus reduce the chance of explosion if the product is to be used around volatile substances.
In the plastics world, this is a material that has had the colour pigments, fillers, or additives included before it arrives at the injection moulder. This can improve consistency but often leads to either a higher cost or a larger minimum order quantity.
A concentrated mixture of pigments or additives which are held in a carrier resin and added to the polymer just before it is moulded.
The choice of plastic used in your project is your decision but our technical team can advise you in choosing the appropriate material for the part and its use, contact us to start discussing your project with our technical team.
How can we support your project?
Together we determine the best design, material and production decisions for optimum quality, speed and value.