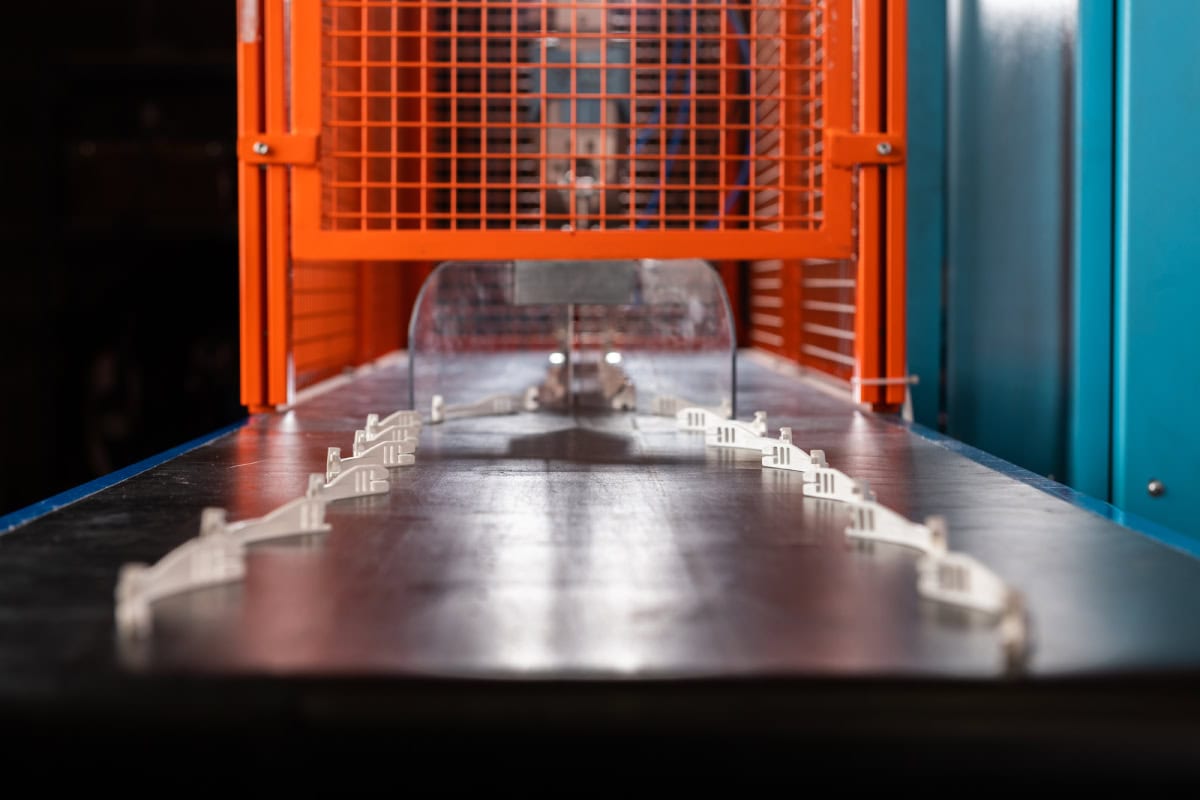
So, you've designed a product, and you're ready to take it to market. Now, you need to decide on the best manufacturing process to bring your product to life.
With so many options available, it can be overwhelming to choose the right one for your specific needs. In this article, we'll explore five plastic manufacturing processes: injection moulding, blow moulding, extrusion moulding, and rotational moulding, as well as 3D printing. We'll discuss the advantages and limitations of each process to help you make an informed decision about which one is right for you.
Plastic Injection Moulding
Plastic injection moulding is a manufacturing process for producing parts by injecting molten plastic into a mould under pressure. The mould is then cooled and the plastic part is ejected.
Our Guide to Plastic Injection Moulding has more information about the process.
This method is ideal for producing high-volume runs of complex and non-complex, three-dimensional parts. Injection moulding is used to produce a wide variety of products, from car parts to medical devices to toys.
The advantages of injection moulding include high production rates, the ability to produce complex parts, and consistency in part quality.
However, the initial tooling costs can be high, making it less economical for short runs or low-volume production.
What are the other Processes and what are the differences?
Other Plastic Processes to consider include:
- Blow Moulding
- Extrusion Moulding
- Rotational Moulding
- 3D Printing
Blow Moulding
Blow moulding is a manufacturing process in which a hollow plastic part is formed by inflating a heated plastic tube inside a mould. Two methods for Blow moulding are Injection and Extrusion Blow Moulding.
This method is ideal for producing hollow parts such as bottles, jars and containers. Blow moulding can produce consistent parts in a wide range of shapes and sizes.
The advantages of blow moulding include low tooling costs and being able to produce high volumes, the ability to produce large parts and complex shapes.
However, there are limitations to design for blow moulding as the process is the best fit to produce hollow bottles and containers.
Extrusion Moulding
Extrusion moulding is a process that involves pushing melted plastic material through a die to create a continuous length of the plastic profile.
This process is ideal for producing products with a consistent cross-section such as pipes, tubing, and window frames.
Instead of an injection moulding tool, a die is used to shape and form the shape of the profile.
It is a highly efficient (there are fewer tool changeovers) and cost-effective process for producing long continuous plastic. There is an investment cost for the die, ranging from £600-£6,000 depending on the size of the extrusion.
Regrind (material recycled from the process) is used a lot more in the process as it is easier to reuse off-cuts.
Due to the process, the plastic profile is warm and malleable for longer and alterations are possible after moulding. However, the profile needs time to cure or it can warp.
Rotational Moulding
Rotational moulding, on the other hand, involves heating a hollow mould and rotating it around two perpendicular axes. Compared to the other processes this is a low-pressure method and this has its advantages.
Instead of using polymer pellets, the material is ground into a powder. The plastic material is then added to the mould, which melts and coats the interior surface of the mould as it rotates. Once the plastic has been cooled by water and solidified, the mould is opened to reveal the finished product.
This method is ideal for producing large, hollow plastic products with uniform wall thickness.
Rotational moulding is also a cost-effective option for low-volume runs, as the moulds are less expensive to create than injection moulds as low pressure is required in the process.
3D Printing
3D printing is an additive manufacturing process that involves creating a three-dimensional object by adding layers of material on top of each other.
The process starts with a 3D design file that is sliced into thin layers, and the printer builds the object layer by layer. 3D printing is a versatile process that can create complex geometries and shapes that are impossible to achieve using traditional manufacturing methods.
The main advantage of 3D printing is that it is quick and cost-effective to produce a small number of parts. You can also make changes to the design without incurring significant additional costs, such as modification of tooling.
Additionally, 3D printing is ideal for prototyping, allowing modifications to be completed quickly and creating customised parts.
However, 3D printing has some limitations. It is not suitable for mass production runs as it is slower and more expensive than other processes. Most 3D printed parts require post-processing to achieve the required finish.
How can we support your project?
We can provide a personalised quote based on your requirements.