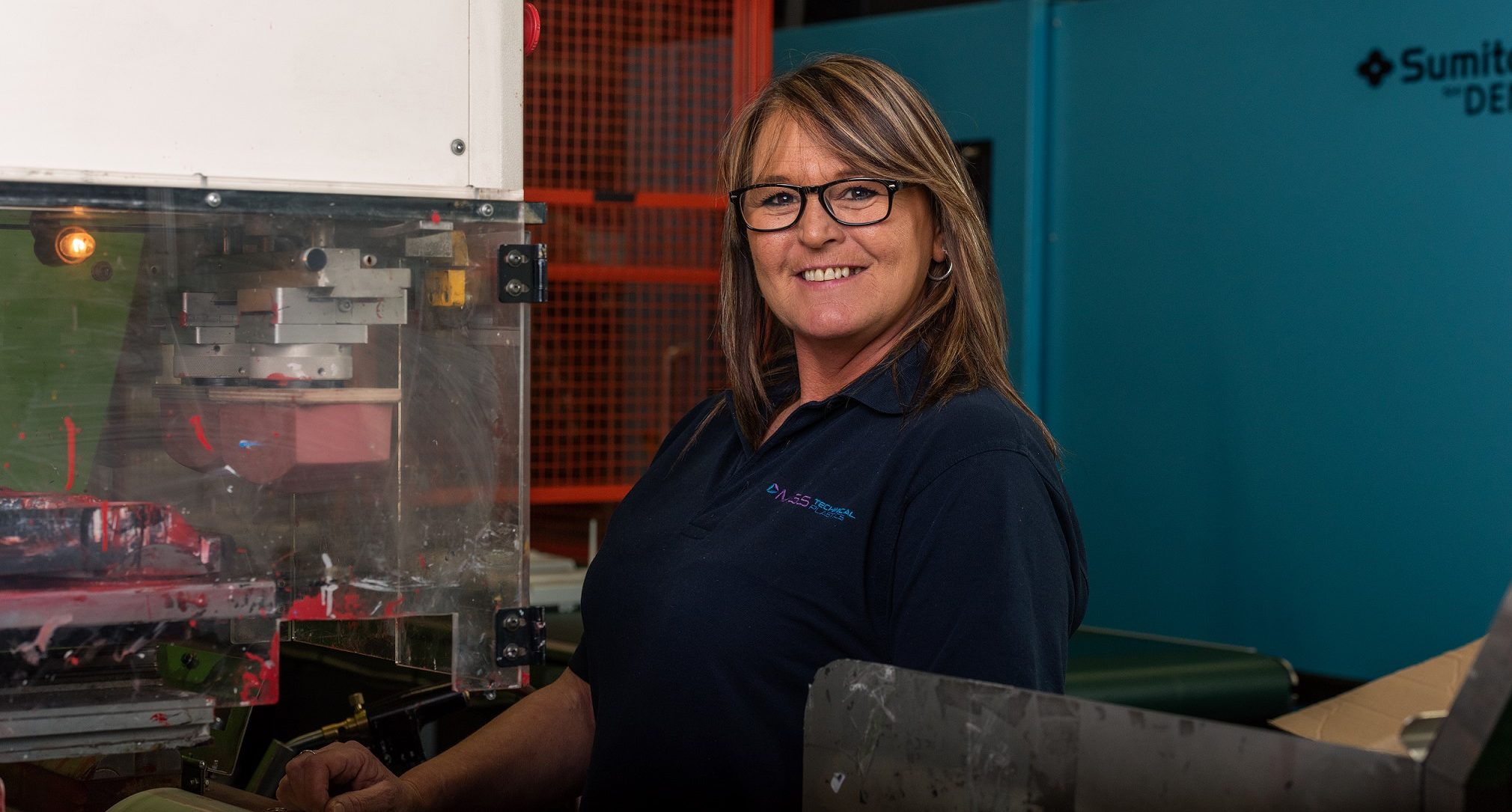
The Blackburn-based manufacturer has introduced a number of initiatives, including upgrades to its factory and improved working practices.
The company has invested significant time in researching, trialling and implementing new and innovative ways to reuse and recycle leftover plastics to become reusable polymers, diverting it from landfill.
The company’s biggest investments to date have been replacing older machines with newer, more energy efficient alternatives. One such purchase, a 900-tonne machine installed last year, is the biggest MGS has ever owned and operated and delivers 40 per cent energy savings compared to its predecessor.
Other initiatives include investing £43,000 in solar panels and converting 90 per cent of the factory’s lighting to low-consumption LEDs, using motion detection in areas visited less often. Motion activated, high speed, roller shutter doors keep more heat in the factory, and help processes become more efficient during the melting process of polymers.
Newly-installed enterprise resource planning software has reduced the amount of paper MGS uses, with any waste paper being shredded to be used at a local animal sanctuary for bedding.
Employees play a key role, too, and in September a team will raise money for charity by completing the 25-mile Three Peaks Challenge in September.
Nathan Sturgess, Procurement Officer at MGS, said: “Sustainability is integral to the working practices of the business. Every member of our team is made aware of our commitment at the outset and encouraged throughout their employment to make ethical decisions that not only go beyond compliance, but positively impact the environment and our stakeholders.
“Our focus on environmental integrity and sustainability is second to none.”
Want to read more? You may be interested in Advocating for Apprentices or Our Manufacturing Excellence Award.